The automotive industry is undergoing a remarkable transformation with the emergence of advanced driver-assistance systems (ADAS) and the promise of autonomous driving, not only revolutionising vehicle usage but also optimising energy consumption on our routes.
Today, vehicles featuring ADAS Level 4, defined as “high automation,” where the vehicle is capable of autonomous travel under normal environmental conditions without requiring driver oversight1, are available on the market. Achieving the safety and efficiency necessary for such systems demands sophisticated sensors and imaging processors capable of providing accurate representations of the vehicle's surroundings, even at high speeds and in unpredictable scenarios.
In recent years, one of the most significant advancements in this domain has been the integration of light detection and ranging lidar systems. Unlike other radar systems, lidar sensors rely solely on light to identify the environment, detecting light reflected by objects using photosensors.
Hamamatsu Photonics, a globally recognised leader in manufacturing optoelectronic components, modules, and systems, has been instrumental in developing lidar solutions for the automotive industry. With more than 70 years of experience in optoelectronics, 30 years of supplying AECQ-qualified components, and three Nobel Prize contributions, Hamamatsu combines extensive expertise with a commitment to continuous research and development.
This article delves into the essence of lidar technology, exploring its core principles, emerging trends, and the critical role of photosensors, unravelling the intricate details that make lidar pivotal in the automotive and broader technological landscape.
Main lidar approaches for automotive applications
Two primary technological approaches dominate lidar: time of flight (TOF) and frequency-modulated continuous wave (FMCW) systems.
While TOF lidar is standard, FMCW systems are gaining popularity for their potential to overcome challenges associated with the time-of-flight approach, particularly in the near-infrared range.
The basic principle of TOF lidar is straightforward: a light source emits a beam of light reflected by obstacles, and the sensor calculates the object's distance based on the time it takes for the reflected light to return.
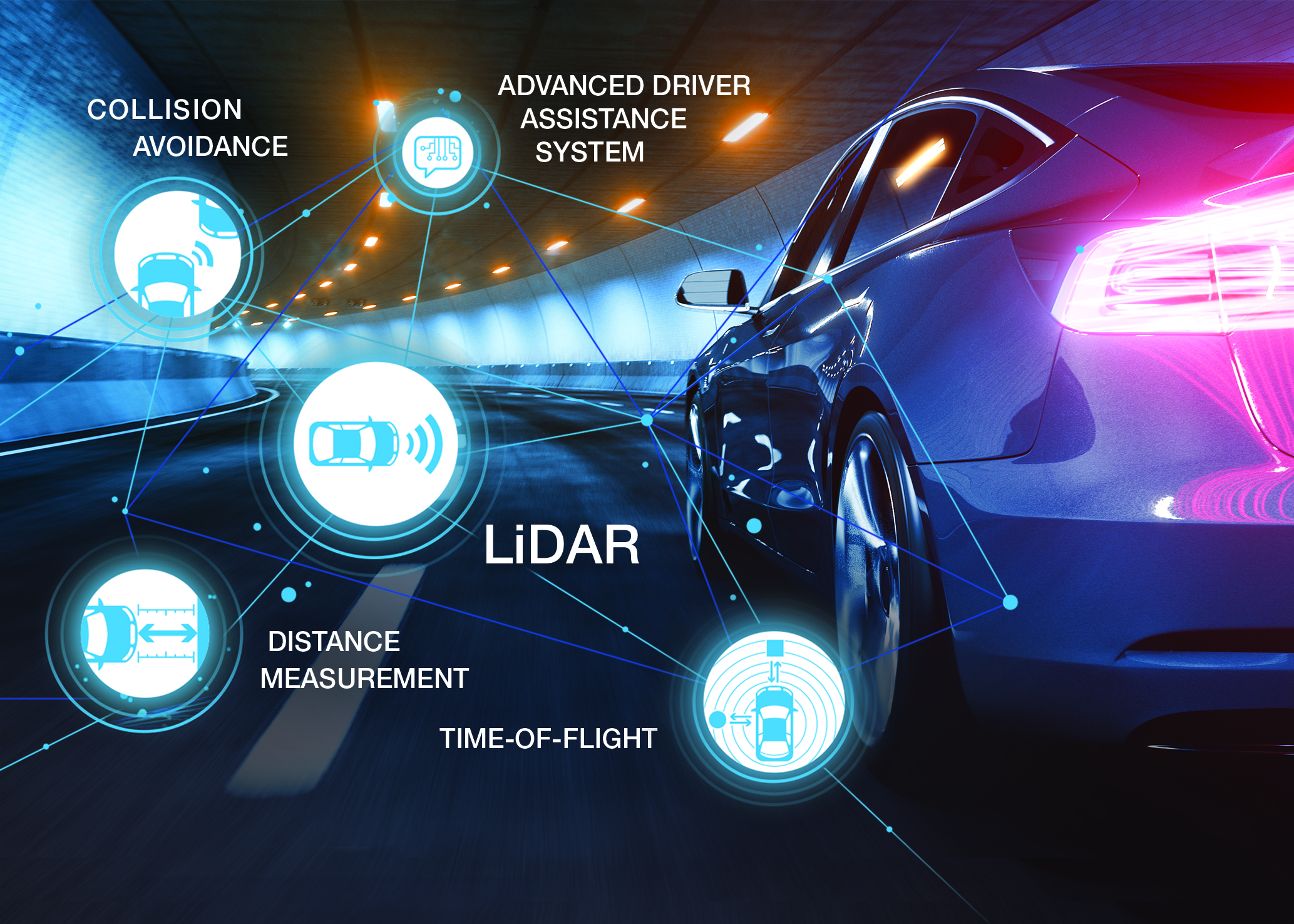
One of the most significant advancements in automotive has been the integration of light detection and ranging lidar systems (Credit: Hamamatsu)
The heart of lidar technology: Photosensors
First, the silicon PIN photodiode (PIN PD) is the most common and simple photosensor with high quantum efficiency and without any amplification, making it ideal for short-range detection due to its lack of gain.
When extending the detection range, it becomes essential to have a sensor with higher gain such as the Si Avalanche photodiodes (APD). It allows for detection in low light conditions and increases the speed of detection.
However, for applications requiring the detection of very low light levels, a device capable of detecting single photons with a high gain becomes crucial. The Multi-Pixel Photon Counters (MPPC), also known as silicon photon multipliers (SiPMs) or single photon avalanche diodes (SPADs), feature a unique structure that effectively reduces noise and enables the detection of each single photon.
Smart sensor integration
While sensor technologies play a crucial role, their capabilities extend beyond light detection to signal processing at the hardware level, offering pre-processed data. Implementing these functions is vital because they allow a reduction in circuit dimensions, increase the robustness of the system, and lower the power consumption – critical factors for the future of electric vehicles.
As most automotive manufacturers have distinct lidar designs, each with their own peculiarities and specialties, a universal “one-size-fits-all” design proves less effective. One of the unique services Hamamatsu focuses on is customisation – not only for the sensor but also for the application-specific integrated circuit (ASIC), which can even be integrated with the sensor through a direct bonding technique. This tailored approach empowers us to help our customers find the best solution for their given application and key requirements.
The future of lidar: Navigating challenges and opportunities
Lidar technology faces challenges such as cost, limited field of view, and standardisation needs2. Addressing these challenges is crucial for realising lidar's full potential in enhancing safety, efficiency, and applications beyond the automotive realms. Despite the hurdles, lidar promises safer transportation, precise drone deliveries, and enhanced robotics capabilities, guided by companies such as Hamamatsu shaping its trajectory.
In conclusion, lidar technology presents a dynamic landscape with immense potential. Hamamatsu Photonics continues to drive lidar's evolution through innovative solutions, customisations, and a commitment to addressing challenges. Beyond technological advancements, Hamamatsu embraces its responsibility to contribute positively to humanity, society, and the environment. As the automotive industry embraces autonomous driving, lidar emerges as a cornerstone technology, guided by companies such as Hamamatsu towards a future of enhanced safety, efficiency, and technological possibilities, mindful of broader societal and environmental implications.
References
1https://caradas.com/levels-of-autonomous-driving-all-levels/
2https://www.linkedin.com/pulse/vehicle-lidar-market-insights-players-fo…
Further information
Find out more about Hamamatsu Photonics’ range of optoelectronic solutions for automotive lidar by visiting the company's website.