Looking for a competitive advantage, INEOS Britannia and engineering company Renishaw collaborated on the design of bespoke parts for the British team’s boat, using additive manufacturing.
The America’s Cup is a 150-year-old boat race. One which, despite having five-time Olympic medallist Ben Ainslie leading their team last time out, a British team has never won. Using AC75 racing yachts equipped with some of the world’s leading technology, the boats reach speeds of 60mph.
“The Amercia’s Cup is a design and engineering competition as much as it is a race,” said INEOS Britannia’s manufacturing manager Michel Marie. “We cannot build a winning boat using off-the-shelf components. Building bespoke parts demonstrates our engineering expertise, as well as making drastic improvements to the boat.”
Key components to the boat’s design such as its rudder, foil wings and bowsprit all have a huge effect on performance, as does the boat’s overall weight. Therefore, producing these bespoke parts from carbon fibre and other advanced materials was crucial to improving its speed and ability to handle the harsh racing environments it would encounter.
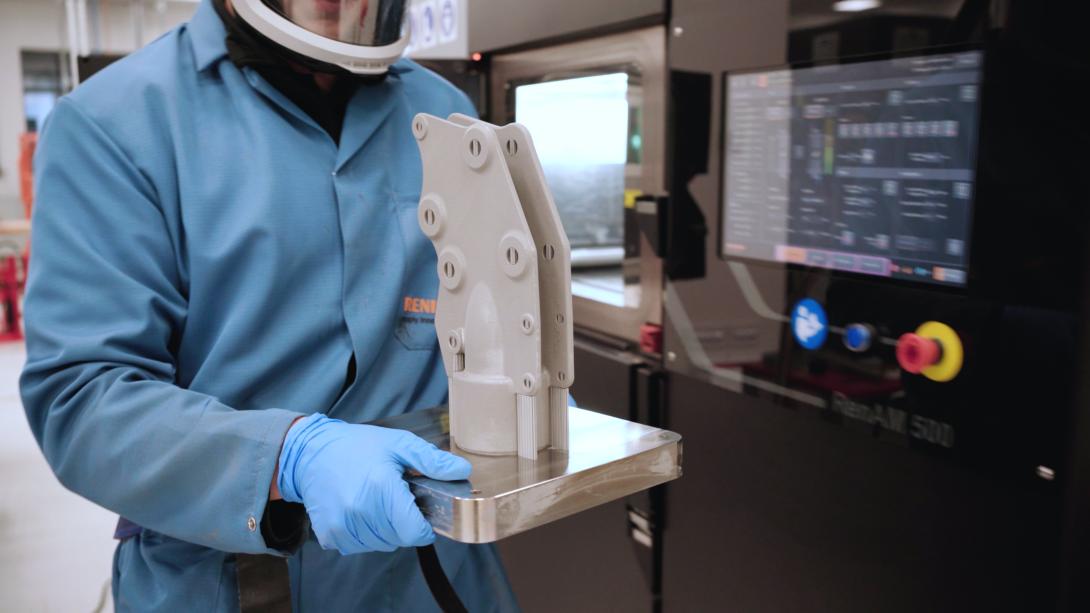
Image: Renishaw
Testing the prototype
After finding an issue with the structural load on the bowsprit during the development of the prototype boat, INEOS knew that specifically prototyping an end detail for the bowsprit would be beneficial, and additive manufacturing (AM) – due to its “ability to produce components rapidly and precisely,” said Renishaw AM customs applications manager Chay Allen – “was an obvious candidate.” But the sacrificial support required to build such a part with overhanding features, proved problematic.
Design for Additive Manufacturing (DfAM) a solution
By integrating additive manufacturing into the design process at an early stage, the parts themselves became better suited to the AM process. The DfAM technique was crucial in overcoming the overhanging problem, for example, as Renishaw engineers could change the part’s orientation on the build plate, so that support was only required in critical areas.
Using four 500W lasers, Renishaw’s additive manufacturing system, Renishaw was able to make bespoke changes to other parts easily, such as adding 22mm to the runner beam end-fitting to clamp it securely, adding T-shaped supports to the foil flap fairings to stiffen the structure and prevent distortion and 10mm diameter support pillars to the outhaul sheave box to prevent peeling from the stress of the melting process.
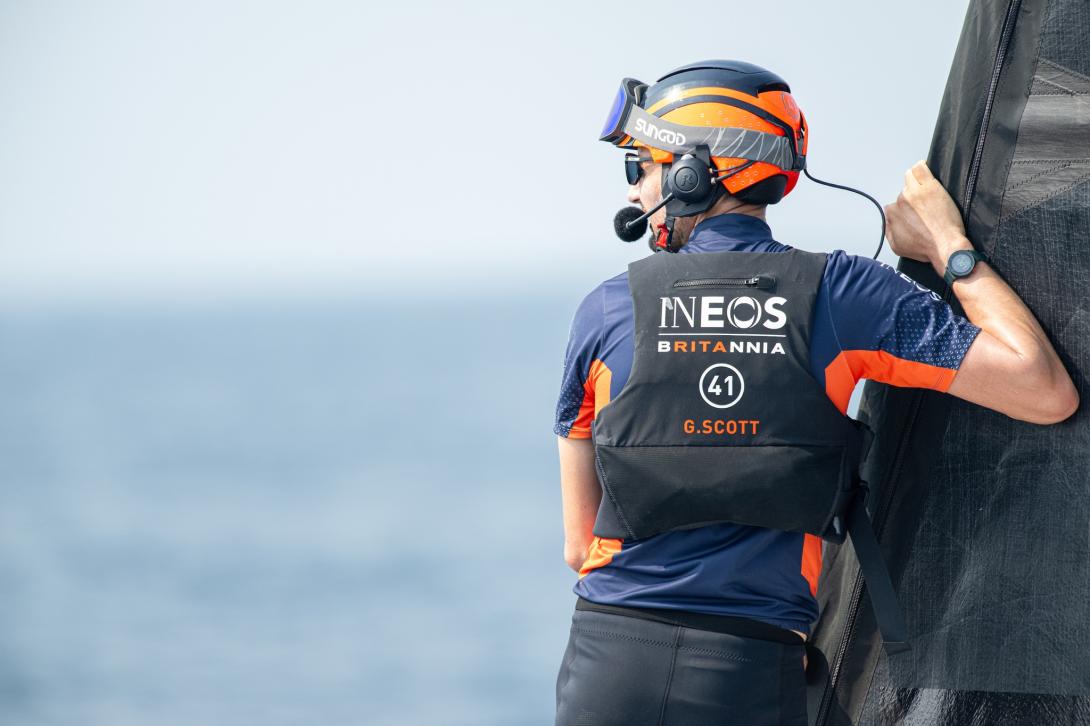
Image: Renishaw
Long-term results
With the America’s Cup Challenger Series 2024 taking place from 28 August - 5 October 2024, the final result of the race is not yet known, but the result of INEOS Britannia’s partnership with Renishaw and introduction to the process of design for additive manufacturing could prove to have more long-term benefit.
“The partnership taught us how to adapt designs to make our final parts better suited to the AM process,” said Nye Davis, INEOS Britannia’s procurement project engineer. “The most important lesson our engineering team learned from the project is to consider the processes and time required to take a CAD file to a finished product.”