With manufacturers globally looking to increase accuracy while reducing wasted materials, photonic equipment is being turned to, for more granular measurements and production. Capable of going down to sub-micron levels, lasers combined with visualisation software are bolstering end-to-end efficiency, with strain being reduced on manufacturing plant staff and their resources.
The global additive manufacturing market is projected by Research Nester to grow from $19.8bn in 2023 to $180.6bn by 2036. This forecasted growth is being driven by the research, development and evolution of photonics-based additive manufacturing methods. These include directed energy deposition (DED), fused deposition modelling (FDM), stereolithography (SLA), and selective laser sintering (SLS).
Here, we explore how these various types of additive manufacturing technologies are being applied, as well as how they can best be deployed and maintained for optimal results.
Additive manufacturing challenges to overcome
The market research published by Research Nester cites the high cost of 3D printers – ranging from $300,000 to $1.5m – as a significant challenge towards the adoption of additive manufacturing, depending on the chosen materials. Along with the costs of shifting from traditional equipment, there are also ever present knowledge gaps and regulatory and certification requirements to consider. Additionally, particular applications bring their own unique pitfalls.
“For metal SLM, the challenge is that the optical performance characteristics need to have the precision of optical instrumentation, but with the reliability and robustness characteristics of a machine tool. This makes metal AM an exciting space for us,” says Rob Brown, Principal Optical Engineer at Renishaw Additive Manufacturing. Renishaw is the official precision measurement and additive manufacturing (AM) partner for INEOS Britannia, the team currently challenging for the America’s Cup in Barcelona, Spain.
The inability of Raman lasers to melt titanium provides a further challenge: the manufacturing of optical assemblies with high power tolerance. This isn’t only the case for high damage threshold optics, but also low absorption glass and coatings to prevent thermal lensing or beam distortions.
Brown continues: “Increasingly, manufacturers are questioning whether a gaussian profile is the correct beamshape to use, particularly for filling in large areas. The jury is out on what shape and technology will prove the most successful, but it will need to be cost-effective and scalable if it’s to meet the industry's aspiration of further displacing subtractive and casting methods of manufacture.”
Directed Energy Deposition (DED) for metal printing
Directed energy deposition (DED) technology is a widely adopted method of metal printing that is helping to optimise production of individual parts. A nozzle mounted on a multi-axis arm deposits metal powder or wire onto a part, before the material is melted using a laser, electron beam or plasma arc.
Use cases involving DED technology that are in high demand among manufacturers include maintenance, repair and operations (MRO); and laser overcoating and cladding.
“The biggest ROI for DED is in the repair business, and this is seen within the automotive, aerospace and energy sectors,” says Robert Yusin, CEO of 3D printing company Optomec, which works closely with a global provider of jet engines on turbine blade repair, as well as with a global automotive manufacturer on motorcycle part production.
According to Yusin, refurbishing and repairing turbine blades for aerospace and energy customers provides cost savings of around 80% compared with creating new blades. Multiple blades can be worked on at once with the aid of automation software, which isn’t possible with traditional welding.
“We work on fixing blades in the hot section and cold section of the engines, and are able to provide ROI back to a production customer in about 1.7 years. You really have three ways to repair a blade: traditional welding; wire bonding; and then our focus, additive powder, to repair a blade. The efficiency comes from the process and CAD software, combined with the hardware that produced the output for the customers.”
DED additive manufacturing is carried out through melting of metal powder, using lasers. Up to four powder feeders are used to accurately produce metal material with optimal properties for properly repairing blades and other engine parts, as well as parts of vehicles.
Different sizes of blades call for the use of various DED machines. At one end of the scale, smaller blades are repaired with CAD-based automation using Optomec’s CS 250 machine, which includes a 250mm x 250mm x 250mm work envelope, and 3-5 axis CNC control system. The optics of the 500-2,000W fibre lasers are customisable using a deposition head, allowing for a variety of spot sizes and power density to be maintained remotely.
Meanwhile, the largest blades are repaired by the CS 558 (500W to 3kW laser, 356 x 356 x 558mm work envelope and three, four or five axes of simultaneous motion).
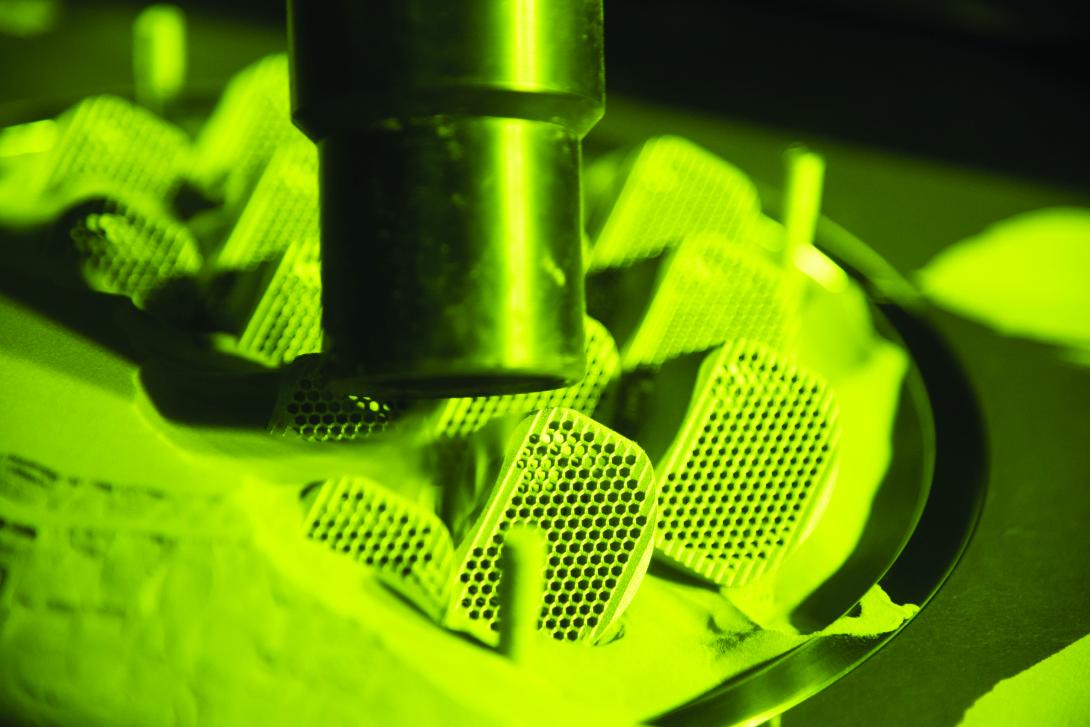
Lasers, electron beams and other light sources are instrumental in helping manufacturers bolster existing parts, as well as efficiently repurposing materials (Image: Trumpf Group)
SLA and SLS for electroplating
There are also certain photonic AM methods that prove valuable for electroplating – the coating of parts with a thin metal layer that is permanently forged to the part via electrolysis. When electronically charged, positively charged ions (or cations) follow the current and deposit a metal layer.
This kind of AM is most commonly used for copper, nickel, gold, silver, palladium, tin, zinc and palladium. As for photonic applications to facilitate electroplating, there are stereolithography (SLA), and selective laser sintering (SLS). SLA uses liquid resin to print parts, while SLS uses thermoplastic powder.
“SLA is generally the easiest to plate because most prints come out fully dense so there is no issue with porosity but it is imperative that the surfaces be clean and fully cured,” said Sean Wise, president and founder of electroplating specialists RePliForm.
“SLS prints generally have some porosity so a good operator will choose print parameters that will make the outer skins of the part watertight. You also get a better bond to sintered/fused parts with photopolymer. The resolution is much better with photopolymer if finish is important to you.”
According to Wise, more than 90% of plastic parts that are electroplated are cosmetic applications, which is prominent in the automotive industry. AM parts are coated to impart an electromagnetic barrier, or for grounding. Additionally, the use of AM permits making parts with thinner walls than you can do with moulding, although these walls can prove flimsy.
To mitigate this, Wise says: “One under-utilised aspect of electroplated coatings is that the deposited film has mechanical, electrical and thermal properties equivalent to wrought copper and nickel, so parts are predictably stiffened and strengthened, and you get better heat conduction around the surfaces when they are plated.”
Vat Photopolymerisation
Away from printing using metal powder, another avenue towards 3D-printed parts is through Vat photopolymerisation. This produces polymers in layers, using ultraviolet (UV) light that granularly creates parts from photopolymer resin stored in a vat. As the build platform is lowered, the UV light cures the resin layer by layer.
Structural support is not present with this method, unlike powder-based applications where unbound material provides this. However, Robert Chimenti, assistant professor and photonics coordinator at Rowan University, says that vat photopolymerisation with digital light processing (DLP) technology can provide a fuller picture, while facilitating tighter focus on smaller prints, leveraging greater resolution in the process. Unlike SLA which traces a layer, DLP can cure the whole layer at once.
Chimenti explains: “In a vat, you can better control the layer-by-layer conversion, helping to achieve more uniform print properties across the Z axis of the part.
“With filament printing or direct ink write printing, you're limited to printing individual voxels, which depends on whatever the Z resolution (layer height) of the stepper motor stage is. It also depends on how you're projecting your light.
“With stereolithography, I can definitely focus a 400nm laser a lot tighter than I can focus an infrared laser, to melt some metal, so I can get smaller spot sizes there. But really, what I'm a big proponent of is DLP technology, because you can project a full XY image into your vat and cure the entire layer, each at a time. And then, in that case, it really just comes down to the optical resolution of your DLP system, which can get down into the tens of microns.
“With the DLP projectors, you also get greyscaling, so you don't have to expose every layer, or even every pixel in every layer for the same amount of time.”
Recent research conducted at Rowan University, presented at Photonics West this year, explored the possible use of partial polymerisation to produce gradient-index (GRIN) lenses. By studying the refraction index, and applying a conversion prediction model based on accumulated light dosage, a needed layer-by-layer light exposure can be determined for more consistent (albeit “not perfect”, according to Chimenti) polymer properties and focal points throughout.
Chimenti added: “Normally when you create a GRIN optic, you place a chunk of glass into a vat of liquid salt, and you time the process depending on how many dopants you have radially. You’re often limited to radial symmetry.
“We now don’t need to print a radially symmetric lens. We’ve printed triangles, squares and the letter R.”
Measuring AM processes and optimising results
Applications involving lasers and other light sources will continue to evolve and make additive manufacturing processes more efficient. Whether printing metal or plastic parts, it’s vital to tailor optical solutions to your specific use case, and apply the right methods accordingly.
“To effectively implement metal 3D printing, manufacturers need reliable and precise monitoring tools like spectrometers. These devices are capable of performing inline measurements across various industrial processes, ensuring consistent and accurate analysis throughout long-term additive manufacturing,” says Martijn van de Goor, technical support engineer at spectroscopy solution provider Avantes.
“By integrating optical emission spectroscopy (OES) into the production workflow, manufacturers can maintain process stability, improve quality control, and ensure consistent output. The precision and reliability allow for detailed spectroscopic analysis that goes beyond basic data, offering deeper insights that are crucial for optimising and refining the 3D printing process.”
Yusin comments: “There is a lot of training that goes into overcoming uncertainty around shifting from traditional methods to additive manufacturing. We’ll usually go through a series of POC [proof-of-concept] iterations before a porosity and operational testing phase, and slowly integrate that into their mainstream.
“It’s really a crawl, walk and run strategy that helps to cross the chasm between prototyping and production.”
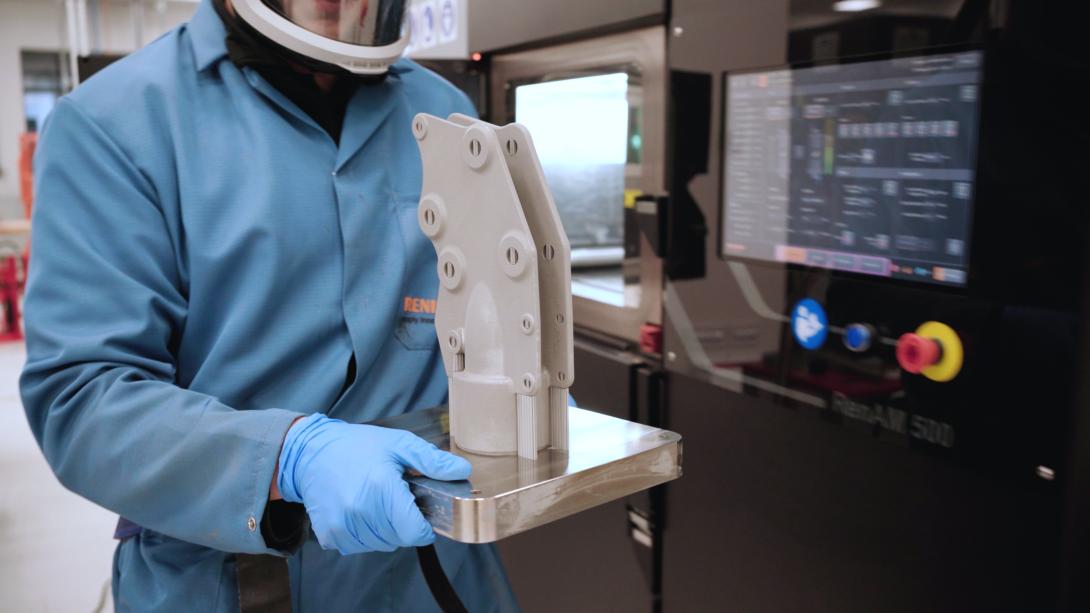
All the parts were built on the RenAM 500Q metal AM system, which uses four 500W lasers to 3D print using a bed of titanium Ti6Al4V ELI-406 metal powder (Image: courtesy of Renishaw)
How AM helps Brittania to (hopefully) rule the waves
INEOS Britannia, this year’s British challenger in The America's Cup, partnered with Renishaw on the 3D printing of crucial parts on the high-tech, high-speed sailboat.
The 75-foot foiling monohull ‘Britannia' will be able to reach speeds of up to 50 knots – over 60 miles per hour. Critical components, such as the boat's runner, flap fairings (covers that help to improve the hydrodynamic performance of the boat’s foils), bowsprit and outhaul sheave box, all influence speed, efficiency and other performance factors.
“The America's Cup is a design and engineering competition as much as it is a race – we cannot build a winning boat using off-the-shelf components,” says Michel Marie, Manufacturing Manager at INEOS Britannia. “Building bespoke parts, such as the unique runner beam fitting and outhaul sheave box, demonstrates our engineering expertise, as well as making drastic improvements to the boat.”
The team availed of Renishaw’s expertise for the design and printing of the parts. When developing the foil flap fairings, for example, the team added T-shaped supports to stiffen the structure and prevent distortion. The supports were designed to taper, reaching a thickness of 0.3 mm when in contact with the part, which enabled easy snap-off removal.
All parts were built on the RenAM 500Q metal AM system using titanium Ti6Al4V ELI-406 metal powder, a material that offers high corrosion resistance and has a good strength-to-weight ratio. The RenAM 500Q system contains four 500 W lasers that are able to access the entire powder bed simultaneously, improving productivity and lowering cost per part.
“The partnership with Renishaw taught us how to adapt designs to make our final parts better suited to the AM process,” explains Nye Davis, Procurement Project Engineer at INEOS Britannia.