Optical freeform surface components have become increasingly popular in recent years for the benefits they bring in terms of design freedom and compact size.
It is important when it comes to the manufacture of freeform optics to achieve high precision in accuracy of optical surface generation. Because of the advantages of these often complex surfaces, the applications for which they can be used have also grown, including aerospace, computer science, defence, electronics and medical, to name just a few.
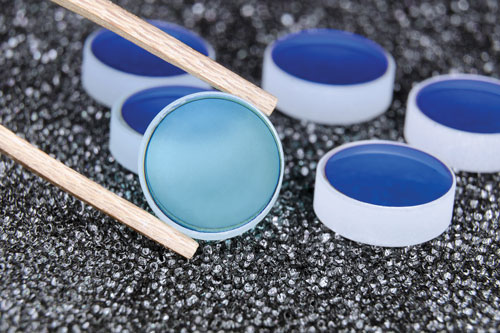
Freeform optics need to achieve high-precision accuracy of optical surface generation (credit: Yury Zap/Shutterstock.com)
However, the design and processing difficulty of some of these components have limited their even wider application potential. Diamond turning has been used in more recent years to provide an efficient method for processing these optical freeform surfaces. The technique uses an extremely precise machining process that generates desired surface profiles with accuracies of a few nanometres or less, and as well as its sub-micron accuracy it can also create nanoscale surface roughness and boasts good controllability.
Dan Musinski, vice president strategic business development at Precitech, believes diamond turning is beneficial to the manufacturing of freeform optics because it provides a stable platform. 'It has the ability' he said, 'to deterministically cut steep slopes and concave features to shape with minimal part stresses and low sensitivity to thermal drift. A unique feature of single-point diamond turning (SPDT) for freeform part generation is the ability to create a set of optical axis references (fiducials) in the same set-up for a non-symmetric shape, which is critical for the alignment of the free form for metrology and within the optical system.'
New opportunities
The company has seen an increase in the application of multi-axis, ultra-precision SPDT, which Musinski attributes to a rise in requests primarily for applications that need to address the manufacturing of more complex optical shapes. What's more, continued developments in precision manufacturing machinery are opening up new opportunities all the time. Fast tool servos (FTS), for example, provide a rapid method to fabricate freeform surfaces, such as light management micro-structures, toric optics, and even mechanical features in contact lenses, lens arrays and laser collimators.
FTS cutting, said Musinski, is also typically 10-15 times faster than other servo tool-cutting methods, such as XZC machining, and so can help customers to improve efficiency and productivity. 'Our fast tool servo is a high-precision machining solution that is faster than other methods while providing excellent surface form accuracy and low waviness,' he said. 'We have also introduced a new feature in our software called Adaptive Control Technology for automated machine tuning, which provides additional throughput and accuracy improvements. The low thermal sensitivity and proprietary integrated vibration isolation solutions of the machine tools are key aspects of our enabling technology. These advances enable rapid manufacturing of high-precision optical surfaces that previously could take many hours to manufacture.'
As with any growing technology, diamond turning is not without its challenges. One of the key challenges, according to Musinski, is the ability to accurately quantify some of the more complex shapes being demanded by new emerging applications. 'The multi-axis DT instruments can manufacture a wide range of complex shapes,' he explained, 'but it is important to have a reliable and accurate means of verifying the shape of the part that has been cut. We work closely with our sister companies within Ametek, Zygo and Taylor Hobson to ensure we have the required solutions for characterising the surfaces with a sufficient uncertainty to ensure high confidence in the results.'
A time to skill
One of the other big challenges to industry when it comes to diamond turning is the current shortage of skilled machine operators. This is something industry and academia are trying to work together to solve. For Precitech this has involved the supply of equipment to educational institutes, such as the recent delivery of a Nanoform X ultra-precision diamond turning lathe to the Technology, Design and Safety Center (TDS Center) at Keene State College in New Hampshire.
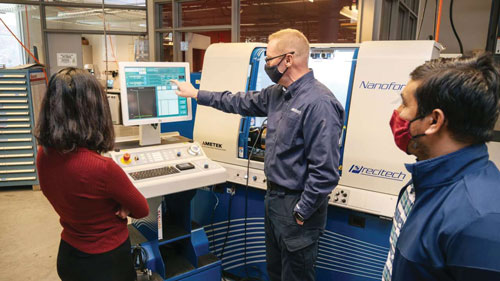
Precitech supplied a Nanoform X ultra-precision diamond turning lathe to the Technology Design and Safety Center (TDS Center) at Keene State College
The 53,000 square foot academic facility is home to the Regional Center for Advanced Manufacturing, which provides manufacturing training and experience for employees in the region. It is considered a national model for preparing undergraduates to fill positions in the manufacturing and construction trades and, as such, incorporates a number of features that enhance its high-intensity programs, such as teaching laboratories, studios, tiered and flat-floor classrooms, shop and critique spaces, as well as a first-floor 'hub' area and a full scale contained environment for safety training. The diamond-turning machine will be used by the college to teach students in Sustainable Product Design and Innovation classes, such as its course in ultra-precision manufacturing.
Lisa Hix, Keene State College associate professor of sustainable product design and innovation, said the machine would 'help students prepare for a range of career opportunities as they learn about and experience the capabilities of ultra-precision machining used in the field of advanced research, medical and automotive industries, and in communication and aerospace applications.'
Importantly, Hix described the technology as 'an important part of a new Optics and Precision Manufacturing Programme at Keene State College\'92. This programme was created in collaboration with industry partners to develop the talents needed in the industry's workforce. It will allow many high-precision companies in the area that produce components and equipment to grow and meet industry demand, in part through the skilled workforce pipeline being developed.'
Keith Kowalski, vice president and business unit manager at Precitech, said: 'We are delighted to help strengthen the local ultra-precision machining community by partnering to train the next generation right here in Keene.'
Also based in Keene is Janos Technology, which has been producing precision infrared optics since the 1970s. The company has also partnered with Precitech, and uses two Precitech Nanoform 350 and One Nanoform 200 diamond-turning machines for high-precision manufacturing of parts up to 14 inches in diameter. The Nanoform machines use Precitech's Ultrapath machine control system, fully constrained hydrostatic boxways, and 8.6nm resolution linear glass scales for positioning. This allows Janos Technology to offer precision refractive, as well as reflective, optics. Surface contours include plano, paraboloids, ellipsoids, hyperboloids, spheres, flats, waxicons and axicons. Although the limits of manufacture vary from one configuration to another, said the company, obtainable and verifiable specifications include figure accuracy to 1/10 λ per inch. Typical surface roughness values range from 4-12nm RMS, depending upon material and configuration.
Keene is also home to the Corning Specialty Materials facility, which houses one of the largest diamond-turning manufacturing operations. The company's diamond-turning process produces surfaces with reduced or eliminated diffraction effects, thereby eliminating the need for post polishing which, in turn, reduces manufacturing time and costs. Optical systems manufactured in this way can also be used in military, aerospace and commercial applications including tactical aircraft targeting, night vision, missile guidance, hyperspectral imagers, helmet mounted displays, medical, analytical instrumentation and semiconductor optics manufacturing.
Training day
Monroe Community College in Monroe County, New York, is working to help industry up- and re-skill in diamond-turning and other techniques, with the launch of a new optical fabrication laboratory. The facility has already seen four advanced manufacturing workers and an MCC student spend their summer gaining some of these specialised skills, including five weeks of training using a $300,000 diamond-turning lathe.
Employers in the region have been finding it difficult to recruit skilled optics technicians who are able to set-up and operate such a machine. Through MCC's workshop, local businesses have been training employees to use this technology. Participants can learn how to program and set up the lathe to perform operations that require a high level of accuracy, as well as the fundamentals of metrology, using different tools to verify that a part was manufactured properly. Students who started MCC's optical systems technology programme this autumn term have already had their first opportunity to use the lathe, as well as other high-tech advanced manufacturing equipment worth more than $1.5m.
The college believes that diamond turning is an important area for optics, with manufacturers purchasing more of these machines for which demand is very high when it comes to technicians who know how to correctly use them. The goal of the new programme is to train people so they can take advantage of the skills they have learned to benefit their employers and customers. Speaking to local news outlet, Monroe Post, Alexis Vogt, programme chair and professor of optical systems technology, whose team developed the workshop, said: \'91Manufacturing companies are trying to buy more of these machines and, ultimately, they need technicians who know how to properly use them. Optics technicians with diamond-turning experience are in incredibly high demand across the U.S.'
As a provider of optical components, Edmund Optics (EO) has been using SPDT for some time. The company uses the technique to produce off-axis parabolic (OAP) mirrors, off-axis elliptical (OAE) mirrors, and other precision metal, plastic and crystalline optical components. It allows the firm to ensure that off-axis focusing mirrors be free of aberrations across a broadband range, which is ideal for use in instrumentation and laser systems. Off-axis parabolic mirrors can be designed using diamond turning to ensure low scatter in the visible spectrum, with a surface roughness of less than 5nm, for use in technology such as spectrometers, interferometers, astronomical optical instruments, spectrum analysers, as well as beam expanders.
EO uses diamond turning in three grades: commercial (λ wavefront error and 80-50 surface quality); precision (λ/2 wavefront error and 60-40 surface quality) and high precision (λ/8 wavefront error and 40-20 surface quality). Using the technique, RMS surface roughness values can also be achieved as low as 3nm
The challenges
In terms of the challenges associated with using diamond turning to produce freeform optics, environmental conditions are a factor, as they can significantly affect the accuracy, performance and lifetime of diamond-turning equipment. Diamond-turning cells must have strict controls in place for temperature, cleanliness and vibration. Machines such as the one used by EO should have built-in vibration control systems to counteract this.
Data collection during inspection should also be thought about to accurately monitor surface quality, surface roughness and mechanical inspection. A variety of metrology instruments inspect the diamond-turned parts to ensure the highest quality, including interferometers, profilometers and co-ordinate measuring machines. In addition to the large selection of standard optical components, EO offers build-to-print or custom capabilities to meet exact customer specifications. EO's diamond-turning staff have extensive experience in optimising designs for manufacturability and cost reduction.
The company believes that processes should be a priority for components providers, including Six Sigma and Lean processes, so that they and their customers can benefit from reduced set-up time, increased lot sizes and minimised waste. An in-house machine shop, including diamond-turning capabilities, will help these businesses allow for more efficient creation of tooling and blanks, further reducing lead times.
Looking to the future, and whether diamond-turning machinery could be improved, opening up even wider application potential, Precitech's Musinski said: 'We must continue to focus on driving new technologies and capability for customers based on their need and the needs of key industries. We are confident in our ability to evolve our products with our team of precision-engineering experts and close cooperation with our corporate partners.'
Laser-assisted diamond tooling: the marriage of optical and mechanical design
Advances in various high-tech markets has increased the demand for high-precision, reliable manufacturing techniques. Ultraprecision diamond machining (UDM) has emerged as a viable commercial solution in addressing such needs and has proven to be integral in realising modern products.
As with any production work, much attention has been paid to optimising the manufacturing chain to reduce the associated costs and increase productivity. At the shop level, typically the idea is to enhance the fabrication process through three key objectives: (1) development of more capable machining hardware; (2) design and manufacture of better tooling: and (3) optimisation of the machining process parameters. Here we review the work done by the Micro-LAM group and its subsidiaries, M10 Edge and 603OPTX, in fulfilling these three objectives.
Laser-assisted machining (LAM)
Assistive machining hardware has been an active area of research and development in recent years. The Micro-LAM technology leverages the emission of a laser beam through a transparent tooling medium, whereby directing the laser beam towards the cutting edge of the tool and on the cutting zone. The absorption of the laser beam by the material undercut is dissipated in the form of heat. This generated heat is meant to alter the surface properties in a way that eases the cutting action. The reduced cutting forces provide the opportunity to cut the material at higher feed rates, as well as increased tool life.
Optomechanical tooling design
A cornerstone of the LAM process is the ultraprecision optomechanical diamond tools (OMDT) that (a) have sufficient mechanical strength for machining hard and brittle materials, and (b) guide the laser through the tooling medium targeting the cutting zone.
The tool's mechanical design is controlled by the rake face angle, flank face angle, nose radius and so on. These geometrical attributes are selected based on three main variables: (1) the substrate material; (2) geometry of the target optic; and (3) ease of fabrication of the OMDT.
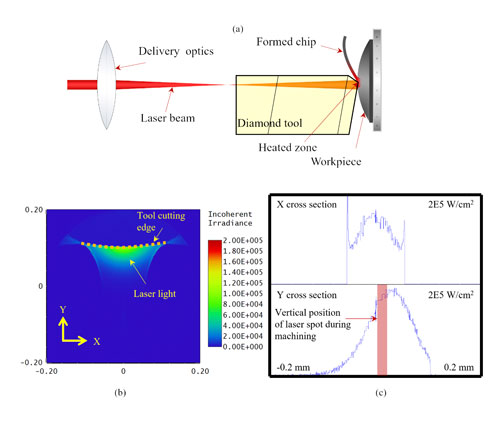
Figure 1: Machining binderless WC (a) machined part (b) surface form measurement (c) surface roughness measurement (d) SEM image at 500◊ magnification (e) SEM image at 20k◊ magnification
The tool's optical design is primarily dictated by the need for delivery of the laser through the diamond. The design should be such that the new tooling doesn't pose any significant challenge in aligning the laser beam. In addition, the laser must be delivered in a very localised fashion to avoid any bulk heating of the material. Heating in bulk can result in the appearance of undesirable form errors. Figure 1(a) depicts the laser delivery through an exemplary OMDT, while figure 1(b) and (c) show the laser spot exiting the OMDT in 3D and 2D views respectively.
OMDT fabrication
The OMDT manufacturing process is a multi-step procedure that needs to be carried out quite systematically. The diamond, generally, has two critical faces that need to be polished optically for transmission of the laser beam. The diamond is brazed on a metal alloy shank under 50kPa pressure and a temperature of 850°C that doesn't cause diamond instability and/or graphitisation.
Upon completion of the brazing process the diamond is ground to the specified nose radius using a diamond impregnated cast-iron grinding wheel. The final tool nose has a cylindrical shape. The roundness, as well as residual waviness on the cylindrical nose, is measured using high-precision instrumentation. Typically, waviness values are less than 250nm.
The Micro-LAM process
The optomechanical tooling and the LAM technology are combined and retrofitted on commercial UDM\'92s to constitute the Micro-LAM process. The Micro-LAM process is developed for brittle materials by tweaking the machining dynamical parameters, type of coolant, as well as the amount of laser irradiation to optimise the cutting process. Various studies have been carried out to demonstrate the efficacy of the Micro-LAM process in cutting hard and brittle materials.
An example of successful implementation of LAM is the machining of binderless WC optics, see Figure 2(a). Figure 2(b) and (c) show surface form (irregularity < 7nm RMS) and roughness (<2nm RMS). High magnification scanning electron microscope (SEM) images in figure 2(d) and (e) provide evidence of the generated smooth surface.
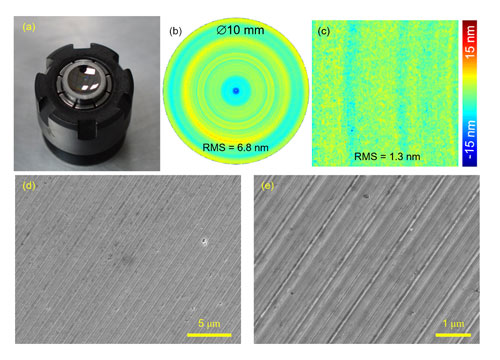
Figure 2 Machining binderless WC (a) machined part (b) surface form measurement (c) surface roughness measurement (d) SEM image at 500◊ magnification (e) SEM image at 20k ◊ magnification
In closing, new machining hardware and processes can improve production of high-precision components and it is incumbent upon us to investigate pathways in achieving such a goal. At the Micro-LAM group, a complete cycle from R&D on equipment, to tooling development, and finally transfer to the shop floor, is realised concurrently. This chain enables direct feedback and optimisation and hopefully will lead to opening new opportunities for the fabrication community.