All About Aspheric Lenses
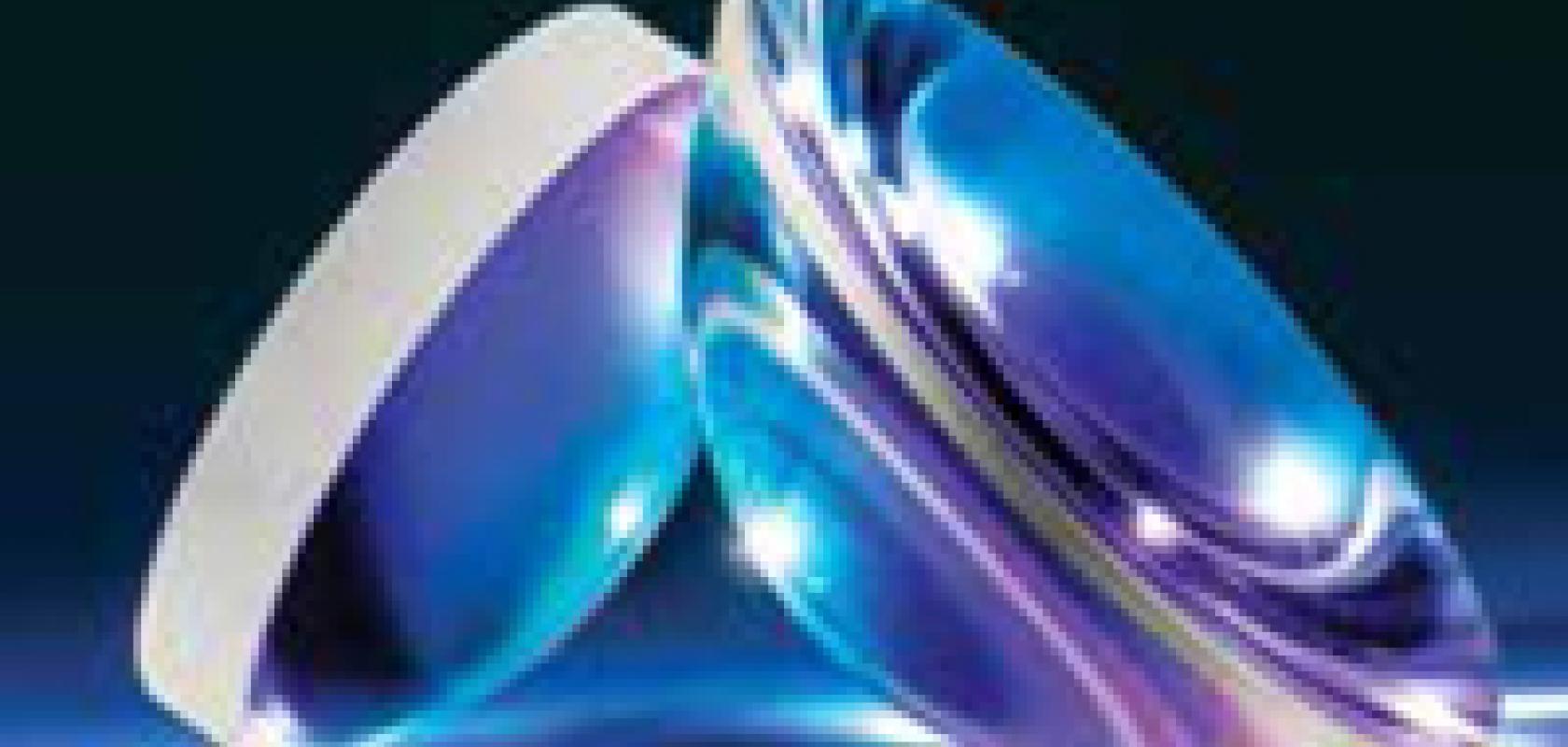
Spherical Aberration Correction
The most notable benefit of aspheric lenses is their ability to correct for spherical aberration. Spherical aberration results from using a spherical surface to focus or collimate light. In other words, all spherical surfaces suffer from spherical aberration independent of alignment or manufacturing errors; therefore, a non-spherical, or aspheric surface, is needed to correct for it. By adjusting the conic constant and aspheric coefficients, an aspheric lens can be optimized for maximum cancellation of aberrations. For example, consider Figure 1 which shows a spherical lens with significant spherical aberration compared to an aspheric lens with practically no spherical aberration. In a spherical lens, spherical aberration causes incident light rays to focus at different points, creating a blur; in an aspheric lens, light focuses to a point, creating comparatively no blur and improving image quality.
To get a better idea of the difference in focusing performance between an aspheric lens and a spherical lens, consider a quantitative example of two comparable lenses with 25mm diameters and 25mm focal lengths (f/1 lenses). The following table compares the spot size, or blur size, of on-axis (0° object angle) and off-axis (0.5° and 1.0° object angles) collimated, monochromatic light rays of 587.6nm. Since a smaller spot size indicates better performance, it is clear to see that the aspheric lens produces much better image quality by two orders of magnitude compared to an identical spherical lens.
Additional Performance Benefits
Although various techniques exist to correct aberrations caused by spherical surfaces, none match the imaging performance and flexibility that aspheric lenses provide. Another technique used includes increasing the f/# by “stopping down” the lens. Although this can increase image quality, it also reduces the amount of light throughput in the system, thereby leading to a tradeoff between the two.
On the other hand, when using aspheric lenses, additional aberration correction makes it possible to design high throughput (low f/#, high numerical aperture) systems while simultaneously maintaining good image quality. The image degradation from a higher throughput design can be sustained because a slight tradeoff in image quality can still outperform a spherical system. Consider an 81.5mm focal length, f/2 triplet lens (Figure 2) consisting of all spherical surfaces versus the same triplet with an aspheric first surface where both designs use the same glass types, effective focal length, field of view, f/#, and total system length. The following table quantitatively compares modulation transfer function (MTF) @ 20% contrast of on-axis and off-axis collimated, polychromatic light rays at 486.1nm, 587.6nm, and 656.3nm. The triplet lens with the aspheric surface shows increased imaging performance at all field angles, indicated by high tangential and sagittal resolution values, by factors as high as four compared to the triplet with only spherical surfaces.
System Advantages
Aspheric lenses allow optical designers to correct aberrations using fewer elements than conventional spherical optics because the former gives them more aberration correction than multiple surfaces of the latter. For example, in zoom lenses where ten or more lens elements are typically used, one or two aspheric lenses can be substituted for a handful of spherical lenses in order to achieve similar or better optical results, minimize the overall cost of production, as well as reduce system size.
An optical system with more elements can negatively affect both optical and mechanical parameters, contributing to higher priced mechanical tolerances, additional alignment procedures, and increased anti-reflection coating requirements. All of these may ultimately decrease total system utility because of the necessity for increased support components. As a result, incorporating aspheric lenses (though higher priced than similar f/# singlet and doublet lenses) can actually reduce overall system design costs.
ANATOMY OF AN ASPHERIC LENS
An aspheric lens, also referred to as an asphere, is a rotationally symmetric optic whose radius of curvature varies radially from its center. It improves image quality, reduces the number of required elements, and lowers costs in optical designs. From digital cameras and CD players to high-end microscope objectives and fluorescence microscopes, aspheric lenses are growing into every facet of the optics, imaging, and photonics industries due to the distinct advantages that they offer compared to traditional spherical optics. Aspheric lenses have been traditionally defined with the surface profile (sag) given by Equation 1:
As they have increased in popularity, there is now a more technically accurate way of describing the surface:
When the aspheric coefficients are equal to zero, the resulting aspheric surface is considered to be a conic. The following table shows how the actual conic surface generated depends on the magnitude and sign of the conic constant k.
The most unique geometric feature of aspheric lenses is that the radius of curvature changes with distance from the optical axis, unlike a sphere, which has a constant radius (Figure 3). This distinctive shape allows aspheric lenses to deliver improved optical performance compared to standard spherical surfaces.
HOW ARE THEY MADE? TYPES OF ASPHERES?
Precision glass molding
Precision glass molding is a type of manufacturing technique where optical glass cores are heated to high temperatures until the surface becomes malleable enough to be pressed into an aspheric mold (Figure 4). After several hours of cooling the cores to room temperature, they maintain the shape of the mold. Until recently, the technology was not available for lenses greater than 10mm in diameter, but new tools, optical glass, and metrology processes have all aided in the advancement of precision glass molding. Creating the mold has high initial startup costs because it has to be precisely made from very durable material that can maintain a smooth surface and take into account any shrinkage of the glass cores in order to yield the desired aspheric shape. However, once the mold is finished, the incremental cost for each lens is lower than that of standard manufacturing techniques, making it a great option for high volume production.
Precision polishing
Grinding and polishing one aspheric lens at a time has been the standard manufacturing technique, but continually increasing technological advances now allow for previously unattainable levels of accuracy. Most notably, computer controlled precision polishing (Figure 5) automatically adjusts the tool dwell parameters to polish away high spots where more polishing is needed. If higher quality polishing is required, magneto-rheological finishing (MRF) is used to finalize the surface (Figure 6). MRF technology provides high performance finishing in less time than standard polishing techniques because of its precise control of the removal location and high removal rate. While more specialized manufacturing techniques require specialized molds, polishing utilizes standard tooling which makes it the primary option for prototyping and low volume production.
Hybrid molding
Hybrid molding begins with a standard spherical surface, such as an achromatic lens, which is then pressed onto a thin layer of photopolymer in an aspheric mold to give the net result of an aspheric surface. The technique uses a diamond ground aspheric mold and a glass achromatic lens (though other types of singlet or doublet lenses can be used). A photopolymer injection is introduced into the aspheric mold, against which the achromatic lens is pressed. The two surfaces are compressed and UV cured at room temperature to yield an aspherized achromatic lens that combines the optical properties of the constituent parts: chromatic and spherical aberration correction. Figure 7 overviews the process of creating a hybrid lens. Hybrid molding is useful for high volume precision applications where additional performance is required and the quantity can justify the initial tooling costs.
Plastic molding
In addition to the aforementioned manufacturing techniques for glass, there exists one unique technique for plastic. Plastic molding involves injecting molten plastic into an aspheric mold. Since plastic is not as thermally stable and resistant to pressure as glass, it has to be treated specially in order to create a comparable aspheric lens. Nevertheless, plastic is advantageous because it is light-weight, easily molded, and can be integrated with a mount to create a single piece. While the selection of optical quality plastic is limited, the cost and weight benefits sometimes drive designs toward plastic aspheric lenses.
ADVANTAGES FOR EACH TYPE OF ASPHERE
Since all applications do not use the same lenses, selecting the appropriate aspheric lenses is an important decision. The main driving factors to consider are volume and cost. Once those two are decided upon, it is easy to pick which aspheric product is the right one. While stock aspheric components are available for immediate delivery or with short lead times for any application budget, they are only available in certain sizes, focal lengths and coating options. If off-theshelf products are not sufficient, consider custom aspheric manufacturing for prototype, pre-production or large volume applications.
CUSTOM ASPHERIC MANUFACTURING CAPABILITIES
NB: For a larger view of this table, download a pdf of this white paper here
Spherical Aberration Correction
The most notable benefit of aspheric lenses is their ability to correct for spherical aberration. Spherical aberration results from using a spherical surface to focus or collimate light. In other words, all spherical surfaces suffer from spherical aberration independent of alignment or manufacturing errors; therefore, a non-spherical, or aspheric surface, is needed to correct for it. By adjusting the conic constant and aspheric coefficients, an aspheric lens can be optimized for maximum cancellation of aberrations. For example, consider Figure 1 which shows a spherical lens with significant spherical aberration compared to an aspheric lens with practically no spherical aberration. In a spherical lens, spherical aberration causes incident light rays to focus at different points, creating a blur; in an aspheric lens, light focuses to a point, creating comparatively no blur and improving image quality.
To get a better idea of the difference in focusing performance between an aspheric lens and a spherical lens, consider a quantitative example of two comparable lenses with 25mm diameters and 25mm focal lengths (f/1 lenses). The following table compares the spot size, or blur size, of on-axis (0° object angle) and off-axis (0.5° and 1.0° object angles) collimated, monochromatic light rays of 587.6nm. Since a smaller spot size indicates better performance, it is clear to see that the aspheric lens produces much better image quality by two orders of magnitude compared to an identical spherical lens.
Additional Performance Benefits
Although various techniques exist to correct aberrations caused by spherical surfaces, none match the imaging performance and flexibility that aspheric lenses provide. Another technique used includes increasing the f/# by “stopping down” the lens. Although this can increase image quality, it also reduces the amount of light throughput in the system, thereby leading to a tradeoff between the two.
On the other hand, when using aspheric lenses, additional aberration correction makes it possible to design high throughput (low f/#, high numerical aperture) systems while simultaneously maintaining good image quality. The image degradation from a higher throughput design can be sustained because a slight tradeoff in image quality can still outperform a spherical system. Consider an 81.5mm focal length, f/2 triplet lens (Figure 2) consisting of all spherical surfaces versus the same triplet with an aspheric first surface where both designs use the same glass types, effective focal length, field of view, f/#, and total system length. The following table quantitatively compares modulation transfer function (MTF) @ 20% contrast of on-axis and off-axis collimated, polychromatic light rays at 486.1nm, 587.6nm, and 656.3nm. The triplet lens with the aspheric surface shows increased imaging performance at all field angles, indicated by high tangential and sagittal resolution values, by factors as high as four compared to the triplet with only spherical surfaces.
System Advantages
Aspheric lenses allow optical designers to correct aberrations using fewer elements than conventional spherical optics because the former gives them more aberration correction than multiple surfaces of the latter. For example, in zoom lenses where ten or more lens elements are typically used, one or two aspheric lenses can be substituted for a handful of spherical lenses in order to achieve similar or better optical results, minimize the overall cost of production, as well as reduce system size.
An optical system with more elements can negatively affect both optical and mechanical parameters, contributing to higher priced mechanical tolerances, additional alignment procedures, and increased anti-reflection coating requirements. All of these may ultimately decrease total system utility because of the necessity for increased support components. As a result, incorporating aspheric lenses (though higher priced than similar f/# singlet and doublet lenses) can actually reduce overall system design costs.
ANATOMY OF AN ASPHERIC LENS
An aspheric lens, also referred to as an asphere, is a rotationally symmetric optic whose radius of curvature varies radially from its center. It improves image quality, reduces the number of required elements, and lowers costs in optical designs. From digital cameras and CD players to high-end microscope objectives and fluorescence microscopes, aspheric lenses are growing into every facet of the optics, imaging, and photonics industries due to the distinct advantages that they offer compared to traditional spherical optics. Aspheric lenses have been traditionally defined with the surface profile (sag) given by Equation 1:
As they have increased in popularity, there is now a more technically accurate way of describing the surface:
When the aspheric coefficients are equal to zero, the resulting aspheric surface is considered to be a conic. The following table shows how the actual conic surface generated depends on the magnitude and sign of the conic constant k.
The most unique geometric feature of aspheric lenses is that the radius of curvature changes with distance from the optical axis, unlike a sphere, which has a constant radius (Figure 3). This distinctive shape allows aspheric lenses to deliver improved optical performance compared to standard spherical surfaces.
HOW ARE THEY MADE? TYPES OF ASPHERES?
Precision glass molding
Precision glass molding is a type of manufacturing technique where optical glass cores are heated to high temperatures until the surface becomes malleable enough to be pressed into an aspheric mold (Figure 4). After several hours of cooling the cores to room temperature, they maintain the shape of the mold. Until recently, the technology was not available for lenses greater than 10mm in diameter, but new tools, optical glass, and metrology processes have all aided in the advancement of precision glass molding. Creating the mold has high initial startup costs because it has to be precisely made from very durable material that can maintain a smooth surface and take into account any shrinkage of the glass cores in order to yield the desired aspheric shape. However, once the mold is finished, the incremental cost for each lens is lower than that of standard manufacturing techniques, making it a great option for high volume production.
Precision polishing
Grinding and polishing one aspheric lens at a time has been the standard manufacturing technique, but continually increasing technological advances now allow for previously unattainable levels of accuracy. Most notably, computer controlled precision polishing (Figure 5) automatically adjusts the tool dwell parameters to polish away high spots where more polishing is needed. If higher quality polishing is required, magneto-rheological finishing (MRF) is used to finalize the surface (Figure 6). MRF technology provides high performance finishing in less time than standard polishing techniques because of its precise control of the removal location and high removal rate. While more specialized manufacturing techniques require specialized molds, polishing utilizes standard tooling which makes it the primary option for prototyping and low volume production.
Hybrid molding
Hybrid molding begins with a standard spherical surface, such as an achromatic lens, which is then pressed onto a thin layer of photopolymer in an aspheric mold to give the net result of an aspheric surface. The technique uses a diamond ground aspheric mold and a glass achromatic lens (though other types of singlet or doublet lenses can be used). A photopolymer injection is introduced into the aspheric mold, against which the achromatic lens is pressed. The two surfaces are compressed and UV cured at room temperature to yield an aspherized achromatic lens that combines the optical properties of the constituent parts: chromatic and spherical aberration correction. Figure 7 overviews the process of creating a hybrid lens. Hybrid molding is useful for high volume precision applications where additional performance is required and the quantity can justify the initial tooling costs.
Plastic molding
In addition to the aforementioned manufacturing techniques for glass, there exists one unique technique for plastic. Plastic molding involves injecting molten plastic into an aspheric mold. Since plastic is not as thermally stable and resistant to pressure as glass, it has to be treated specially in order to create a comparable aspheric lens. Nevertheless, plastic is advantageous because it is light-weight, easily molded, and can be integrated with a mount to create a single piece. While the selection of optical quality plastic is limited, the cost and weight benefits sometimes drive designs toward plastic aspheric lenses.
ADVANTAGES FOR EACH TYPE OF ASPHERE
Since all applications do not use the same lenses, selecting the appropriate aspheric lenses is an important decision. The main driving factors to consider are volume and cost. Once those two are decided upon, it is easy to pick which aspheric product is the right one. While stock aspheric components are available for immediate delivery or with short lead times for any application budget, they are only available in certain sizes, focal lengths and coating options. If off-theshelf products are not sufficient, consider custom aspheric manufacturing for prototype, pre-production or large volume applications.
CUSTOM ASPHERIC MANUFACTURING CAPABILITIES
NB: For a larger view of this table, download a pdf of this white paper here