Lithium-ion batteries are currently the go-to option for consumer electric vehicles, but they do not meet the needs of the trucking industry, where long-haul journeys and heavy loads are commonplace. Hydrogen fuel cell propulsion systems are being developed to help meet these needs, and lasers play a huge role in their production.
Hydrogen not only offers long ranges and burns cleanly – the only byproduct being water and heat – but vehicles can be refuelled with it almost as fast as petrol/diesel engines, meaning no long waits for batteries to recharge.
Development of hydrogen fuel cell trucks is already being driven by established vehicle manufacturers including Toyota, Daimler, Hyundai and Volvo, as well as by start-ups such as Nikola Motor. Suppliers and OEMs have already begun small-series production of fuel cells. New manufacturing facilities with a larger production capacity are currently under construction or at the planning stage across the globe.
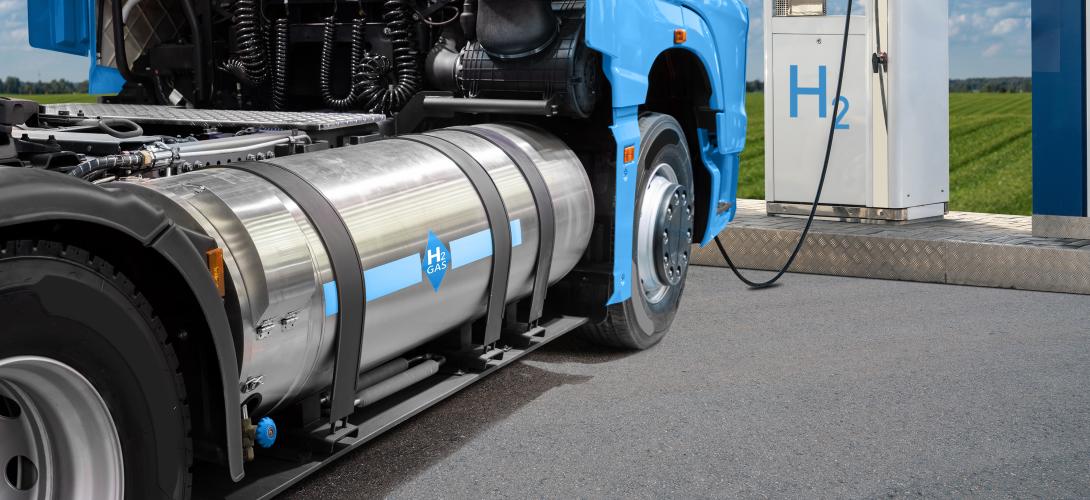
The manufacture of bipolar plates accounts for 28% of the cost of hydrogen fuel cells (Scharfsinn/Shutterstock.com)
The key to unlocking a hydrogen-powered future is mastering the manufacturing of the stack, which unless overcome will keep the manufacturing cost of fuel cells – and consequently the cost of hydrogen-powered vehicles – very high.
These stacks consist of 200 to 500 bipolar plates welded together, and while lasers have the potential to contribute to many stages of the manufacturing process, including the cutting and cleaning of the plates, it is the welding that could potentially have the greatest impact on driving down the cost of producing the cells.
“What limits the industry breakthrough, is that the bipolar plates are a very significant part of the production cost of the fuel cells. There are other challenges of course, such as the scaling up of hydrogen production and the scaling up of distribution and retail, but improving the manufacture of bipolar plates could have the biggest impact on cost reduction, as it currently accounts for 28% of the cost of fuel cells,” said Roi Yaacov, business development manager from Israeli laser manufacturer Civan Lasers.
'The welding process must be of the highest quality'
Each plate is around the size of an A4 sheet of paper and is not much thicker than a human hair. Each of the several hundred plates must be welded together, requiring hundreds of thin seams to be made, each anywhere from three to five metres in length and being barely visible to the naked eye. At a weld speed of 1m/s this would result in a single stack taking up to around 40 minutes to weld, with a medium size car requiring one fuel cell stack and heavier vehicles requiring more.
Most importantly, each weld seam needs to be absolutely gas-tight and perfect. “Even the smallest error would be fatal,” Dr Christian Schmitz, CEO of Trumpf’s Laser Technology. “This is because hydrogen is the smallest molecule in the world, much smaller than natural gas, and it slips through every crack and pore. A single leaky bipolar plate can render a complete fuel cell stack unusable. The welding process must be of the highest quality, and this is best achieved with a laser.”
The welds must be made over complex geometries over a very large area with tremendous accuracy. In addition, stack manufacturers must keep the heat entering the workpiece to a minimum in order to prevent the metal sheets from warping. This stringent list of requirements rules out almost all the available joining processes – apart from the laser.
In recent years the laser industry has mobilised to research and develop new techniques and solutions for perfecting and conducting the complex task of bipolar plate welding.
How to overcome laser weld 'humping'
Civan Lasers, for example, recently commercialised coherent beam combining laser technology to overcome ‘humping’, the physical limit of welding at high speeds. “The laser combines 10s of different lasers, while being able to control the phases of each of the 10s of beams,” said Yaacov. “What this technology permits us to have, besides different levels of power, is a dynamic beam that enables us to produce any arbitrary shape that we’d like to have within the beam. If we’d like to have, for example, a spiral beam, a circle, a doughnut, or whatever beam that you think of, we can, and all without any moving parts. We can change the different parameters, so we can control the melt pool better, and eliminate the phenomena of humping.”
While Scanlab, together with its sister companies Blackbird Robotersysteme and Holo/Or, is developing a novel scan set-up that showed the potential to nearly double the productivity of welding bipolar plates for hydrogen fuel cells.
In March, Blackbird Robotersysteme set up a test rig integrating the 2D scan head intelliSCAN from Scanlab and Holo/Or’s Flexishaper, an adjustable beam shaper. The necessary beam shape was determined based on welding process simulations.
The layout of the beam shaper is the result of a combined optical design, integrating both diffractive optical elements (DOE) and scan system. The processing tests demonstrated to shift the speed limit of failure-free welding speed from 45m/min up to 70m/min.